Definire gli intervalli di manutenzione per le attrezzature di una PMI del settore meccanico
La manutenzione delle attrezzature in una PMI (Piccola e Media Impresa) del settore meccanico è fondamentale per garantire l’efficienza operativa, la sicurezza dei lavoratori e la longevità delle macchine. La definizione degli intervalli di manutenzione appropriati richiede un approccio metodico che tenga conto di diversi fattori, tra cui il tipo di attrezzature, le condizioni operative e le raccomandazioni del produttore.
Oggi ti do qualche suggerimento importante, e poi ricordati di accedere in MyMax Work ed utilizzare le applicazioni che ti fornisco gratuitamente per tenere sotto controllo tutti i tuoi impianti.
Tipi di Manutenzione
Prima di stabilire gli intervalli, è importante comprendere i diversi tipi di manutenzione:
- Manutenzione Preventiva (MP): Interventi pianificati effettuati a intervalli regolari per prevenire guasti.
- Manutenzione Predittiva (MPd): Basata sul monitoraggio delle condizioni dell’attrezzatura e sull’analisi dei dati per prevedere i guasti imminenti.
- Manutenzione Correttiva (MC): Interventi eseguiti dopo che un guasto si è verificato.
- Manutenzione Proattiva (MPa): Focus sull’identificazione e l’eliminazione delle cause profonde dei guasti, migliorando le prestazioni a lungo termine.
Fattori da considerare
1. Raccomandazioni del produttore
Le specifiche del produttore sono un punto di partenza essenziale. Queste raccomandazioni sono basate su test e dati raccolti durante lo sviluppo dell’attrezzatura e offrono una guida iniziale sugli intervalli di manutenzione.
2. Condizioni operative
Le condizioni operative includono fattori come l’uso intensivo, l’ambiente di lavoro (ad esempio, presenza di polvere, umidità, temperature estreme) e i cicli di lavoro. Le attrezzature utilizzate in ambienti più severi richiedono intervalli di manutenzione più frequenti.
3. Storico delle manutenzioni
Un’analisi storica dei dati di manutenzione può rivelare tendenze e modelli nei guasti e nei tempi di inattività. Questo permette di ottimizzare gli intervalli basandosi su dati reali.
4. Monitoraggio delle condizioni
L’implementazione di sistemi di monitoraggio delle condizioni, come sensori per vibrazioni, temperature e livelli di rumore, consente una manutenzione predittiva più accurata, riducendo i costi e migliorando l’affidabilità.
5. Criticità dell’attrezzatura
Non tutte le attrezzature hanno lo stesso impatto sul processo produttivo. È fondamentale classificare le attrezzature in base alla loro criticità e stabilire intervalli di manutenzione prioritari per quelle più critiche.
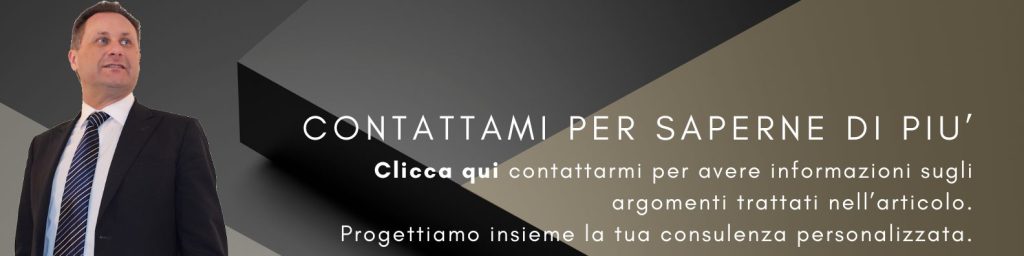
Definizione degli intervalli di manutenzione
Passaggio 1: Raccolta dei dati iniziali
- Documentazione del Produttore: Raccogliere i manuali e le raccomandazioni.
- Storico delle Manutenzioni: Analizzare i registri passati.
- Condizioni Operative: Valutare l’ambiente e l’uso delle attrezzature.
Passaggio 2: analisi dei dati
- Analisi dei Guasti: Identificare le cause e le frequenze dei guasti.
- Monitoraggio delle Condizioni: Implementare sistemi di monitoraggio per ottenere dati in tempo reale.
Passaggio 3: Classificazione delle attrezzature
- Criticità: Classificare le attrezzature in base alla loro importanza nel processo produttivo.
- Rischio di Guasto: Valutare il rischio associato a ciascuna attrezzatura.
Passaggio 4: Pianificazione della manutenzione
- Intervalli di Manutenzione Preventiva: Stabilire intervalli basati sui dati raccolti e sulle raccomandazioni del produttore.
- Manutenzione Predittiva: Utilizzare i dati di monitoraggio per pianificare interventi predittivi.
- Revisioni Periodiche: Effettuare revisioni periodiche degli intervalli di manutenzione basandosi sull’evoluzione dei dati storici e delle condizioni operative.
Passaggio 5: Implementazione e monitoraggio
- Pianificazione Dettagliata: Creare un calendario di manutenzione dettagliato.
- Formazione del Personale: Assicurare che il personale sia adeguatamente formato sulle procedure di manutenzione.
- Monitoraggio Continuo: Valutare costantemente l’efficacia del piano di manutenzione e apportare modifiche basate su nuovi dati e feedback.
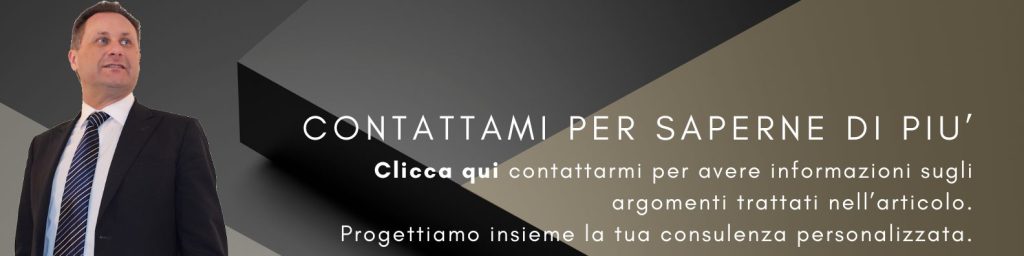
Cosa puoi fare con MyMax Work
Registrati gratuitamente in MyMax Work e utilizza tutte le applicazioni per gestire e mantenere le attrezzature della tua azienda.
Archivia le attrezzature, pianifica le attività di manutenzione necessarie, fatti avvisare delle scadenze, registra le attività svolte, analizza i rischi… e tanto altro ancora.
Non usare più Excel per fare elenchi ingestibili.
Registrati gratuitamente su MyMax Work e inizia subito a lavorare mantenendo efficienti le tue attrezzature.
Conclusione
Definire gli intervalli di manutenzione delle attrezzature in una PMI del settore meccanico richiede un approccio sistematico e basato sui dati. Integrando le raccomandazioni del produttore con l’analisi delle condizioni operative e l’uso di tecnologie di monitoraggio, è possibile ottimizzare la manutenzione, ridurre i tempi di inattività e migliorare l’efficienza operativa complessiva. La manutenzione non è un processo statico, ma deve essere adattata e migliorata continuamente per rispondere alle esigenze dinamiche dell’ambiente produttivo.
Registrati gratuitamente su MyMax Work e inizia subito a lavorare mantenendo efficienti le tue attrezzature.
SCARICA GRATUITAMENTE IL LIBRO
CONTINUAVANO A CHIAMARLA QUALITA’
Ripercorri la storia della ISO 9001
e scopri tante tecniche per migliorare il tuo Sistema Qualità.
Scarica gratuitamente questo mio nuovo libro e poi dimmi cosa ne pensi.